(SPOT Tracker and TruQC have joined forces to become TRU, a Jones Company)
An AMPP (formerly SSPC) QP 1 certification is an essential step in assuring your customers that you have the know-how to apply quality protective coatings capable of withstanding the wear-and-tear of the elements for years to come.
Once you’ve achieved that certification, you wear it like a badge of honor, and rightfully so. It shows that you’ve earned the skills necessary to do the job right. So don’t let a small thing like being unprepared for an audit cause you to lose your certification.
Check out this handy guide to all the bases you need covered in the event of an audit. Hey, maybe even keep a copy in the cab of your truck, or store it digitally in TRU’s Document Library part of TRU’s quality control management software.
What AMPP QP 1 Contractors should have on-site for an audit:
Work control documents and procedures
- A copy of the document authorizing the work, if it hasn’t been sent to AMPP in advance. It may be in the form of a letter of authorization, purchase order, or contract as long as it bares the signature of the client. Contractors are encouraged to attach these to job notification forms.
- A document describing the work to be performed. This should detail specifications for the work and standards requirements. These must be available for examination at the site.
- Documentation of any changes in the work, non-conformities and corrective actions.
- A current list of employees on site and a description of their duties, along with payroll information.
- A document control procedure and documents authorizing employees to act.
- OSHA regulations and a copy of the company’s Mission Statement must be posted.
Safety compliance documents and procedures
- A copy of the company’s site-specific safety and health plan.
- Any accident/injury reports, minutes from safety meetings and documents verifying corrective actions and safety enforcement.
- Documents verifying employees have received the proper safety training for their job assignment.
- Safe operating procedures for all major equipment on site.
Quality control documents and procedures
- A copy of the most recent internal audit.
- A copy of the company’s project-specific quality control (QC) procedures and/or QC plan showing verification of inspection hold points. This plan describes the minimum QC activities that will be independent of the client’s inspector performing QA.
- Product data and SDS for all abrasives, cleaners, paints, thinners and other chemicals used on-site.
- Have inspection reports on-site including actual measurements and readings, in accordance with the company’s project-specific quality control plan.
- Inspection reports or other documents that includes instrument calibration readings and a record verifying periodic calibration.
- Proof of craft training for workers and of formal QC training for QC inspectors.
- Operating procedures and maintenance records for all equipment on-site.
Safety equipment
- Adequate devices and signs for controlling site access, such as caution tape, fences, cones, barricades, etc.
- Adequate sanitation/personal hygiene facilities such as toilets, hand wash facilities, drinking water, etc.
- Provide personal protective equipment in accordance with OSHA regulations, SDS and company safety rules.
- Fire extinguishers, first-aid kits and other emergency management equipment.
Industrial and quality control equipment
- Compressors, pressure washers, blast machines, dust collectors, personnel lifts, paint pumps, spray guns and other industrial equipment.
- Inspection instruments including calibration verification procedures and devices.
- AMPP visual and other job-related standards and procedures.
Other equipment and documents which may be required
- Specialized safety and environmental monitoring equipment.
- Project-specific environmental compliance plan.
- Copy of work-related regulations.
- If this information is not on site at the audit, the contractor must demonstrate document acquisition during the audit.
Learn how an integrated app can help keep you AMPP-certified
Storing all the paperwork and documentation for your AMPP certificate shouldn’t be a headache. TRU can simplify this process by storing your important documents in one central location. Learn more by scheduling a demo with us today.
(SPOT Tracker and TruQC have joined forces to become TRU, a Jones Company)
The formerly SSPC QP 5 certification, now updated with the forming of AMPP, is a must-have for top coatings inspection companies. It carries a lot of weight — many projects exclusively call for QP 5 certified firms — but it’s not easy to earn.
In fact, there were only 14 QP 5 certified companies in the world as B&N Inspection and Supply (BNIS) was gearing up to apply for it.
With the help of TruQC, BNIS became the 15th.
Streamlining the QP 5 certification process
To earn the QP 5 certification, BNIS needed to prove its competence in quality control, inspection practices, internal procedures and more. This ultimately gives their clients peace of mind that its inspectors perform precise and consistent coatings inspections in the field.
To do that, BNIS needed to go through the long application and evaluation process, which would culminate in a day-long, 39-point audit with an SSPC certification specialist.

TruQC transformed this complex process into a simple, digital checklist containing everything BNIS needed to have prepared prior to submitting their application. Throughout the certification process, they stored all relevant documentation on TruQC’s secure, cloud-based platform for easy retrieval.
Beyond just the software, TruQC’s team was an indispensable resource throughout the certification process. BNIS Principal Eric Nenninger says that every time he reached out to TruQC with a question or request, a representative responded with an answer or status update — often within 30 minutes.
SSPC itself uses TruQC to conduct its on-site QP 5 certification audits, so when it came time for the final audit, there were no surprises. Both BNIS and the auditor were working off the same, comprehensive audit checklist. Three months after submitting their application, BNIS earned their QP 5 certification.
Integrating TruQC as a key part of day-to-day operations
TruQC is a process digitalization solution that can be configured to many end uses — helping organizations streamline the industry certification process is just one way to use TruQC.
BNIS has also integrated the TruQC framework into their day-to-day operations. The BNIS team uses the TruQC iPad app to record, store, query and analyze key job-site documentation. They use features such as the daily inspection and safety reports, employee files, specifications, blueprints, expense reports and timesheets.
Instead of performing calculations manually for each report, the inspectors simply enter raw data points and TruQC automatically populates all final calculations. Now, BNIS inspectors can attach photos directly to each report in the app, rather than manually uploading them into a Word or Excel document like they did before TruQC.
All of these process efficiencies add up. BNIS inspectors used to spend several hours a night entering photos and doing calculations to finalize their reports. Now, they leave work at work.
Nenninger estimates that, since partnering with TruQC, each of his employees has saved an average of 10 hours per week filling out and submitting paperwork. In addition, the reports they do submit are more uniform, precise and timely, which his clients greatly appreciate.
Nenninger says that while TruQC is known within the coatings industry as the platform for daily documentation, that’s just the tip of the iceberg. He appreciates being able to store all the information about every project — safety reports, daily inspections, expense reports, timesheets and employee files — in one, secure system.
Let’s talk
We’ve helped hundreds of organizations in a variety of industries rapidly digitalize their reporting and job-site documentation processes. To learn how we can configure our framework to your proven processes and workflows, reach out to our team today.
(SPOT Tracker and TruQC have joined forces to become TRU, a Jones Company)
In the case of digitization and digitalization, two letters make all the difference. This is not merely a matter of wordplay — it’s a matter of scope and potential value to your business. Understanding the distinctions between these two approaches is critical as the digital transformation gains momentum and businesses move toward digital technologies to enhance visibility and eliminate inefficiencies in their operations.
Here, we’ll give a straightforward explanation of both digitization and digitalization, offering examples of each. Then we’ll explore why we designed TruQC as a strategy for process digitalization.

Digitization: Converting data to a digital format
Digitization describes the pure analog-to-digital conversion of existing data and documents. Think scanning a photograph or converting a paper report to a PDF. The data itself is not changed — it’s simply encoded in a digital format.
Digitization can reap efficiency benefits when the digitized data is used to automate processes and enable better accessibility — but digitization does not seek to optimize the processes or data.
Digitalization: Transforming your business processes for digital
As Gartner defines it, digitalization is “the use of digital technologies to change a business model and provide new revenue and value-producing opportunities; it is the process of moving to a digital business.” Digitalization moves beyond digitization, leveraging digital information technology to entirely transform a business’ processes — evaluating, reengineering and reimagining the way you do business.
If digitization is a conversion of data and processes, digitalization is a transformation. More than just making existing data digital, digitalization embraces the ability of digital technology to collect data, establish trends and make better business decisions.
As SAP News points out, you would digitize a document, but you would digitalize a factory. As it pertains to reporting, you would digitize a report — but you would digitalize your organization’s data collection process and workflows.

TruQC: A process digitalization strategy for your business
The TruQC app contains all the integrated features necessary to store key documents (e.g., safety plans, blueprints), collect key data (e.g., reports, flagging issues) and analyze that data for enhanced visibility and business intelligence. All of your documents and data are stored in a secure, digital location, where they’re accessible anywhere, anytime from an internet-connected device
TruQC is a digitalization strategy for your reporting processes. Rather than only collecting and documenting your reports in a digital format (digitization), TruQC empowers you to glean insights and efficiencies from that data by tracking issues and running data summaries (digitalization). The TruQC team can also use APIs to integrate with your management and legacy databases to show how you can learn from this data and use it to update future strategies.
Beyond the app itself, the TruQC team helps organizations take a digital-first approach to reporting, transforming and improving the way they approach reporting to maximize the benefits of digital technology.
A digitalization approach to flagging, tracking and resolving issues in the field
To illustrate how process digitalization looks in practice, let’s narrow in on our issue tracking feature, which we custom-built for a leading oil and gas company. They wanted a better way to flag, track and resolve issues consistently across their assets and projects. Rather than simply converting their current issue tracking process into a digital format, we leveraged the power of digital technology to rethink and transform how they track and resolve problems as they arise. Our issue tracking feature has proven so useful that we rolled it out to all our clients.
We set up the feature so that an inspector could uniquely identify each issue on the blueprint or digital isometric drawing while filling out a report, attaching as many photos as necessary for an admin to understand the problem. An inspector could denote an issue’s type and severity, and schedule any necessary maintenance without leaving the TruQC app. Once an issue has been flagged, admin users can immediately view it and add any notes they may have. Each recommended corrective action is broken into its own report, so admin users can easily track an issue to resolution.
Because this data is collected digitally, it’s easy to filter, download and analyze as needed. It can be sorted by time period, type, severity and project — and because information is entered objectively and consistently, it serves as a point of standardization across your organization. This data can be used to run a pivot table and establish trends, input into your organization’s asset management database and use RBI tools to update strategy or however best allows you to learn from the data and prevent issues in the future.
Our issue tracking feature certainly made it easier to track, resolve and analyze issue data, but the true mark of a digitalization strategy is the opportunity for increasing efficiency and revenue. After reviewing the feature’s impact on this company, we found that it reduced inspection prep, execution, report creating and risk score assignment by 33% globally. Its implementation also resulted in an estimated $1.5 to 2.3 million hard dollar savings per downstream facility. Read more about the impact of a digitalization approach to tracking issues here.
Our issue tracking feature is but one example of how TruQC transforms workflows throughout an organization. By eliminating barriers between the field and office, your organization then works more cohesively and efficiently across projects and assets. To learn more about TruQC, and whether your organization could benefit from a process digitalization strategy, feel free to reach out to our team.
(SPOT Tracker and TruQC have joined forces to become TRU, a Jones Company)
Operators often have to maintain hundreds, if not thousands, of valuable assets at their facility or site at all times. Establishing and following a maintenance schedule can not only become a hassle but can also turn into a drain on both asset utilization and productivity without the proper organizational systems in place.
Effective asset management can help managers keep tabs on each of their assets and corresponding maintenance schedules. Digitalizing these processes, utilizing solutions like TruQC, provides a better way to easily track people, projects, and resources from one platform and enhance your preventative maintenance strategy. But why is it important to use asset management to prioritize preventative over reactive maintenance?
Find out more below about the benefits of preventative maintenance and how it works in conjunction with your asset management solution!
What is the Difference Between Preventative and Reactive Maintenance?
Preventative maintenance is planned maintenance—such as repairs, replacements, adjustments, cleaning, lubrication— all meant to prolong the life of a variety of company assets. Essentially, it is a systematic approach that aims to care for a piece of equipment while it is still running at an acceptable capacity.
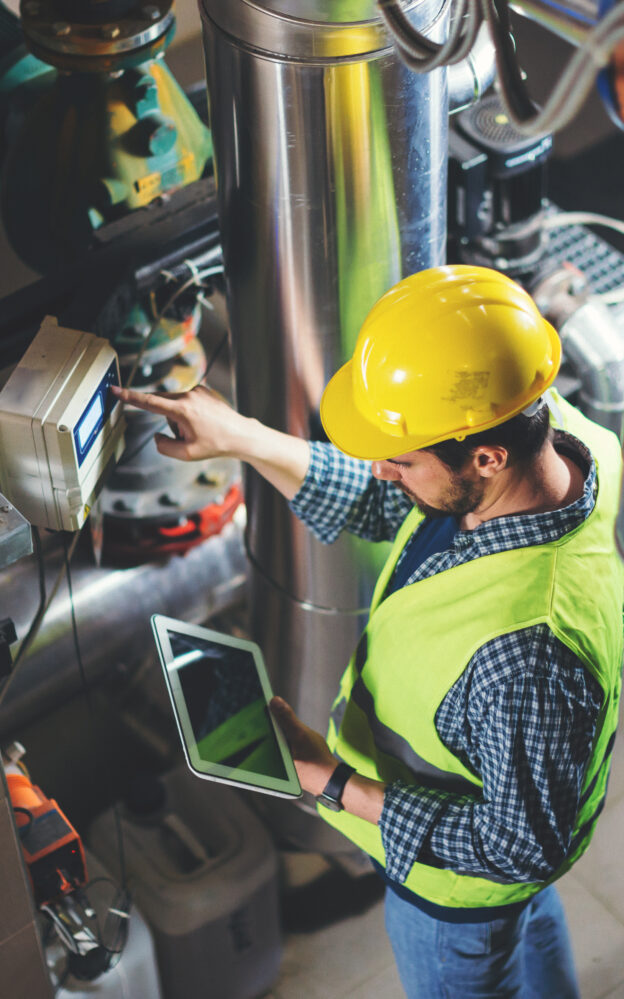
Meanwhile, reactive maintenance usually occurs when the asset has suffered some sort of breakdown that makes it unacceptable for use until repaired or replaced, therefore, you are reacting to problems as they arise. Whether it is a simple malfunction or an entire equipment failure, a maintenance technician identifies the issue and works to restore the asset to operable capacity. Until this happens, the whole process is usually down and the effects are costly.
Machines aren’t built to last forever, which is why reactive repairs are almost inevitable—but steps should still be taken to minimize them and their associated downtime as much as possible. After all, effective asset management often comes down to maximizing asset utilization via proactive (i.e. preventative) maintenance instead of simply reacting to the asset malfunctions as they arise.
So what can you do to effectively reduce reactive maintenance as much as possible? It all comes down to the data!
Data is the Foundation of Maximizing Asset Utilization
Digital records containing good, clean data of the maintenance performed and condition on inspection are both essential to effective asset management and the reduction of reactive maintenance. In order to create these records, you need to digitalize the field and data collection process around asset maintenance so that the data can then be fed into back office systems that are used to analyze metrics, trends, and more.
There are two different ways in which the digitalized data can be used to inform your maintenance strategies:
- Predictive maintenance uses data to predict when an asset will need to be repaired or replaced based on algorithms, artificial intelligence, and other types of data points.
- Preventative maintenance uses data provided by the supplier or machine producer in which they typically recommend a specified amount of time for certain inspections, updates, and more.
By way of an example, let’s say your digital records show that a piece of equipment is due for some preventative maintenance work. You can use asset management software to send notifications for open work that needs attention or to schedule work orders for future maintenance tasks. It’s that simple to seamlessly track asset productivity, condition, and utilization from one digitalized platform.
While data can help you better plan and schedule preventative maintenance, predictive maintenance is not even possible without data. As they work in conjunction with each other, both predictive and preventative maintenance should be prioritized in order to reduce reactive maintenance; that way, businesses spend less time reacting to random asset failures and more time performing data-driven maintenance based on actual asset experience over time. This all works towards the ultimate goals being:
- To empower successful decision-making
- To keep the job site running as smoothly as possible by minimizing downtime and surprises
But these are far from the only benefits of prioritizing preventative/predictive maintenance over reactive. So what else can you stand to gain from preventing problems rather than reacting to them?
Why Preventative Maintenance Over Reactive?
There are many reasons why preventative maintenance should be prioritized over reactive, including but not limited to:
- Minimizing the chance of malfunctions/failures, costly repairs, and unscheduled downtime
- Reducing the risk to people and preventing injuries
- Extending the life of equipment
- Increasing productivity
But the number one reason, put simply, is that it’s merely better to prevent a failure than react to it. This saves your company time, resources and—you guessed it—money down the line.

Example: Predictive/Preventative Maintenance Makes Turnarounds More Efficient, Saving You Money and Reducing Downtime
Let’s say your company is due for another turnaround. The typical turnaround has costs that quickly add up. Every day that your plant is down means you lose out on valuable productivity and revenue. Extending your turnaround maintenance window, even by just a day or two, can be the difference between profits and slipping into the red.
For this reason, a well-planned turnaround process is essential to minimizing downtime, and the best way to ensure this is to use predictive maintenance analytics to inform preventative maintenance strategies. This means using data to predict when an asset will need to be repaired or replaced can help businesses schedule the downtime instead of the downtime being the result of reacting to a problem. This, in turn, allows a company to not only have a more efficient turnaround process, but to also have an increase in both uptime and asset utilization.
Moreover, adequate preventative maintenance leading up to a turnaround primes all of your assets for whatever maintenance work is needed. That way, any third party assisting with the turnaround can get in and get out as efficiently as possible, allowing you to get back up and running ASAP.
(SPOT Tracker and TruQC have joined forces to become TRU, a Jones Company)
In April 2020, SSPC: The Society for Protective Coatings and NACE International announced they would be merging to form a combined organization that we now know as AMPP: Association for Materials Protection and Performance. This merger brings together two organizations with over 145 combined years of experience and expertise in the coatings and corrosion industry. AMPP will be led by two Board of Directors, the AMPP Board and the AMPP Global Center Board.
But, what does this mean for the coatings world? As a coatings or corrosion professional, here is what you need to know about the merger and what it means for your business:
What is AMPP?
The Association for Materials Protection and Performance, AMPP, is the new organization formed from the merging of NACE International and SSPC. The new organization will utilize the corrosion prevention and protective coatings industry expertise brought by SSPC and NACE, while further extending to cover overall protection of assets and performance of materials worldwide.
Headquartered in Washington, D.C., the newly formed AMPP is over 40,000 members in 130 countries consisting of contractors, owners, craftsmen, corrosion experts, manufacturers, and consultants. And with this merger comes the sharing of new coatings technology, resources, answers and ideas on a scale not seen before.
Why did NACE and SSPC decide to merge?
Both NACE and SSPC had a common goal of protecting people, assets and the environment. Member leaders decided that through sharing knowledge and combining proven training, certification, and education programs, they could elevate industry performance and better serve all stakeholders. SSPC’s Board of Governors and NACE International’s Board voted in April 2020 to officially merge the two orgs.
In a press release, SSPC Executive Director, Bill Worms and NACE International CEO, Bob Chalker issued the following joint statement, “From the time each of us began working for our organizations we have believed our members can be stronger together. We are devoted to providing our members with the best services, education, and products possible and we know this combined organization will accomplish that and more. We are pleased to see this come together and look forward to a bright future ahead for the members of SSPC and NACE.”
What are the benefits of a merged organization?
As previously mentioned, this merger brings together two organizations with over 145 combined years of experience and expertise in the coatings and corrosion industry. As a combined organization, AMPP becomes a facilitator for innovation, ensuring improvements in corrosion prevention, risk mitigation, surface preparation techniques, and coatings technology to ultimately elevate the industry as a whole.
“No other association will provide the depth and breadth of materials protection and performance information, standards, education, certification, and contractor accreditation programming that AMPP now provides,” said Tim Bieri, Chair of the AMPP Board of Directors and Vice President for Materials & Corrosion Engineering, in a press release.
How will AMPP make this a smooth transition?
Integration teams and task groups made of members of both organizations have been working together to combine the best aspects of both organizations, providing you with a one stop shop for conferences and accreditation programs. Task groups are bringing together knowledge from the best experts in coatings, corrosion and protection to devise the best in standards, education and certifications.
Further, SSPC and NACE hosted town hall meetings after the announcement of the merger to ensure their members could provide feedback, ask questions, and express concerns along the way. AMPP progress updates and the town hall meeting schedule can be accessed here.
What will change?
As SSPC and NACE merge to form AMPP, it is understandable that coatings contractors have questions about how this will not only affect the industry, but their day-to-day work procedures. To see the full AMPP transition Q&A, go here.
What will happen to my SSPC or NACE membership?
Beginning January 2021, members of both organizations can opt-in to receive dual-membership along with benefits of both organizations at no additional cost. In late 2021, AMPP will release a new membership model featuring multiple levels designed to enable members to select benefits on based personal needs and preferences.
Members of AMPP can now access a unified set of standards and certifications, more resources and information, expanded professional networks, and much more.
More info here.
Will I lose my current SSPC and NACE certifications?
No. All current SSPC and NACE individual certifications will continue to be recognized and supported, eventually merging into a single program.
Until the AMPP certification program is officially launched, any cardholders who need to recertify during 2021 can do so under their respective program. If a candidate holds similar SSPC and NACE credentials, e.g. CIP and PCI, they will need to renew both, but will only pay one renewal fee.
What is going to happen to NACE and SSPC’s contractor accreditation programs?
The QP program established by SSPC will be retained by AMPP and will serve as the basis of the future accreditation program. Elements of NACE’s NIICAP program will be integrated and there will be a transition program for all NIICAP contractors.
AMPP’s new “QP” brand will combine the best elements of the QP and NIICAP accreditation programs to create a new contractor program.
What will the new AMPP standards look like? Will the NACE and SSPC standards still be accepted?
All existing NACE and SSPC standards will continue to be used without change.
What will happen to education courses offered by NACE and SSPC?
AMPP plans to consolidate programs where there is overlap, improve or modify existing courses, and develop new courses covering emerging topics in the industry, such as digital transformation (or digitalization). However, current courses will continue until this process has been completed.
Do I need new software to work with AMPP?
This may depend on what kind of software you are currently using.
Some software is too rigid or vast to adequately adapt to changes in industry standards or practices. Working with an agile, configurable software solution that can be quickly updated to meet the needs of your business ensures success for the long term. Finding digital partners that prioritize your work process is key.
How can I stay up to date on these changes?
Stay informed on AMPP news, transition updates, and register for town hall webinars here.
Upcoming conferences and events news here.
Subscribe to one of their publications or podcasts:
Visit legacy brand websites:
- NACE: www.nace.org
- SSPC: www.sspc.org
“By the time we engaged [TRU] for the flange management portion of our turnaround, we were only 10 weeks from the start of the event. TRU was able to fully digitalize our flange inspection and repair workflow, configuring the solution to our own unique standards and specifications in a tight schedule. We used the solution from start to finish, which allowed us to move away from a qualitative to 100% quantitative decision-making process.”
– Brad Wolters, Reliability Manager, CITGO Petroleum
Like many in the petrochemical industry, leadership at CITGO’s Midwest Refinery Hydrofluoric Acid (HF) Alkylation Unit had experienced previously ineffective attempts to streamline and optimize turnaround processes. Everything from off-the-shelf software to giant whiteboards had been employed with marginal improvement on the outcome. The intensity of the HF alkylation process made the turnaround exceptionally difficult, with the flange inspection, repair and replacement activity being a significant portion of the event. TRU was engaged just 10 weeks prior to the turnaround to digitalize the entire flange portion of the event.
CITGO’s Turnaround Challenges:
- Thousands of flanges to assess and return to service
- Record and track inspection, repairs and overall progress
- Inspections conducted almost completely by third-party contractors
- Only weeks to launch a new solution
Secure, custom configured platform
Tight timeframe or not, IT security is always a hurdle when it comes to implementing new digital technology at any business. TRU (formerly TruQC) cleared this early on, as we do with all our clients, leveraging our detailed Technology Control Plan that demonstrates we meet the most stringent cloud security requirements, including that of the US Navy and Department of Defense based on our work with their contractors.
Further, CITGO engaged TRU based on our solid existing turnaround framework and their confidence in our ability to customize that framework in time for their imminent turnaround. The solution needed to fit their workflow, reflect their processes, and speak in their terminology. Part of this meant it was important to design and build CITGO’s solution by role, so users from different departments could easily get their work done without sorting through extraneous information. The work hadn’t changed for them, just the way they documented it.
TRU calls this configuration, and it’s what sets our digitalization solutions apart from traditionally rigid software. And we don’t just do it for CITGO – every TRU solution is custom configured for our clients.
Fully virtual from Discovery through Implementation
To make sure we properly configured CITGO’s solution, we began with our standard Discovery process, managed by our experienced Project Management team. Our clients benefit from our broad digitalization experience – in both time to configuration and design for usability. CITGO’s turnarounds span multiple departments and often include third-party contractors that enter mid-turnaround, so they needed a solution that was easy to understand and use without a lot of training. Ahead of the turnaround, TRU was able to roll-out a fully capable solution to production and train the initial set of users without having to visit the refinery. Even prior to the limited travel in 2020, TRU had virtually engaged and launched clients across industries, giving CITGO the confidence to stay the course for digitalization with TRU as a partner.
Using TRU start to finish, CITGO was able to control all data related to their flange turnaround because the data belonged to them and was always accessible in real-time. Up-to-date, API-based internal standards were in the hands of every third-party inspector. Real-time access to status and progress was there for every flange, allowing engineering to adjust schedules and repairs on the fly. Wasted visits to flanges that were unopened or not clean enough to inspect were nearly eliminated, as was headcount just to manage paperwork processing. The optimized process allowed the flange portion of the turnaround to finish on time and on budget despite several time-consuming repair surprises along the way.
“[TRU] was intuitive, the user interface was great, training was simple, and everyone could get the data they needed. And that data made the difference – I consider TRU a huge success.”
(SPOT Tracker and TruQC have joined forces to become TRU, a Jones Company)
Digital transformation has gone from a buzzword to common place in most industries, including petrochemical, refining, marine and power generation. Many companies now have some form of digital transformation strategy as an annual budget item, looking to capitalize on its promises of efficiency, transparency, and improved decision making. Further, companies have shifted their business models by heavily investing in digital systems that include risk-based algorithms and predictive analytics, all of which require a wealth of data achieve the goals of a the more digital business. With the operational changes forced by the pandemic, digital technologies are increasingly relied upon to collect and disseminate data in an effort to maintain informed communication as teams work remotely with limited contact.
Recently, Harvard Business Review (HBR) published an analytics survey titled, “Business Successes with a Dual-Track Approach to Transformation” where they defined dual-track transformation in this way: “An approach that simultaneously addresses enterprise-wide transformation as well as the modernization of processes that flow across business workflows and workgroups.” CIOs are increasingly embracing this dual-track approach as they lay out their roadmaps to align new technologies to their companies’ business goals.
TruQC has focused on modernizing business processes via digitalization since its founding over nine years ago, working at the operational level to implement digital tools to optimize client’s workflows and efficiently gather and distribute data. Our clients can quickly implement our solutions to keep up, or catch up, as adopting digital technology becomes the standard rather than the exception. TruQC’s solutions become a key part of our clients’ digital transformation strategy, with the flexibility to adjust as plans mature and change. The HBR survey refers to this flexibility as rapid-cycle innovation, describing it as a “business’s ability to rapidly improve the hundreds of essential processes that cross business workflows and workgroups.” Rapid-cycle innovation is a core building block of any digitalization effort because it focuses on “achieving quick wins for the business, while supporting long-term transformation.” Successful digital transformation relies on new technologies that incorporate both short and long-term business goals.
Optimize Your Existing Processes, Don’t Reinvent Them

Positively impacting processes that involve frontline resources across workgroups requires a deep understanding of what is required to get the work done and how waste or non-value-added effort can be eliminated. It may seem obvious, but empowering field resources and non-IT professionals to create and implement digitalized solutions is an integral part of this effort, particularly for buy-in at launch. This is why TruQC’s digital transformation process starts with Discovery.
We seek to understand how the work gets done today, responding to the suggestions and pain points of each role involved in the process. For most of our customers, compliance is an integral part of their business model. Understanding of and adherence to standards, whether they are industry-wide or internal, are the basis of winning and maintaining business. However, the work needs to get done in an efficient and timely manner with the most current specifications available. We have the know-how to recognize the non-value-added efforts within a workflow and preserve what is required for our customers to continue producing quality work.
The next step in our rapid-cycle digital innovation is made possible by our flexible, cloud-based software platform. TruQC has thousands of building blocks available which are used to custom configure our digitalization solutions. Drawing on the Discovery process, the resulting solution aligns completely with our customers’ existing process. The user interface and permission-based workflow fit how each part of the work gets done for the optimum user experience for each individual role. And because we can quickly handle changing needs in both standards and workflow, we become partners with our customers as they expand their digital transformation strategies.
By now, you can see how compliance becomes a built-in part of the newly digitalized process. Redundant data entry, searching for documents, and spending hours configuring reports are all eliminated while the compliance information is available real-time. Clean, standardized data is a natural product of the solution, available to supervisors, engineers, and existing back-office systems. And access to clean data in one centralized platform lets businesses improve decision making, both in the short and long-term.
Expect Immediate Benefits
When you think of introducing a ‘digital’ solution, your first thoughts may be of lengthy software customization, failed implementation, and no hope of a return on investment. TruQC’s approach ensures this scenario is not repeated.
TruQC is not just a form building software. With your existing business process and standards as the focal point, we leverage a robust and flexible software framework to rapidly deliver a custom configured solution specifically for your process. We optimize what you already do on a daily basis, streamlining data collection and distribution and ensuring the right information is available to all those involved when and where it is needed.
The key to recognizing immediate benefit from a solution is gaining efficiency on an operational level. Often digitalization solutions only focus on corporate needs and fail to take into account the daily operational activity. TruQC’s approach relies on identifying your current processes and workflows and optimizing them, rather than reinventing them.
Digital Reports with Standardized Responses: Decreases reporting time and reducing data entry errors. In a 2018 case study, a top 5 oil and gas company saw a 50% decrease in inspection time after implementing TruQC.
Immediate Report Generation: Eliminates the time spent re-entering data and formatting reports.
Real-Time, Cloud Connected System: Chain-of-command workflow is streamlined as data can be transferred or accessed anytime, anywhere.

Capture Photos In-App, On-Site: Further simplify the reporting process by adding photos directly into your TruQC reports while in the field. No more wasting time uploading and formatting photos after the fact.
Device Integrations with Elcometer and PosiTector: Wireless connection with gauges let you import readings directly into reports, no data re-entry required.
Centralized Document Management System – Accessible Anytime, Anywhere: Drastically reduce the time spent searching for specific data points or documentation, simplifying audits, comp claims, maintenance needs, etc.
Full Offline Capability: Always have access to your digital reporting tool even in the most remote areas. When your device reconnects with cellular or Wi-Fi, all data automatically syncs to the cloud, instantly connecting your operations.
APIs and Integrations to Quickly Connect Your Systems: Move data when and where you want it with APIs and integrations. No need to waste time or resources entering endless amounts of data into existing systems.
All these features result in immediate operational efficiency gains, while still guaranteeing corporate data and compliance needs are met.
Get Started Today
TruQC brings the benefits of a cloud-based application to operational resources in a unique way, overcoming the barriers typically faced when introducing new digital technologies.
Security: All of TruQC’s clients benefit from our work with the US Navy and its Department of Defense (DoD) contractors, as our platform meets the highest DoD cloud solution security standards including NIST CUI 800-171 and FedRAMP.
COVID-19 Safety: TruQC has completed Discovery, configuration, training and launch of our solution 100% remotely for customers throughout the pandemic. We are effective remotely because we focus on the process and the data, drawing on our team’s extensive experience to recognize opportunity and set our clients up for success at launch and beyond.

Adoption: Our intuitive user interface, fully functional offline application and permission-based features provide the optimal customer experience, eliminating potential pushback from users as information and workflows are presented in a way that supports their process, not in a way that requires them to change.
Integration: TruQC’s process digitalization is a key component to an overall digital transformation strategy. TruQC looks to support existing internal platforms such as asset management tools and risk-based software by providing clean, standardized, real-time data to make better informed business decisions.
Experience Our Solutions
Set up a demo today. In a short half hour, we’ll show you examples of our custom configured solutions in action and review your specific process digitalization problems to lay out next steps. Start your journey to successful digital transformation today.
Interested in some of our success stories? Check out our case studies.
(SPOT Tracker and TruQC have joined forces to become TRU, a Jones Company)
Based in Salisbury, MA, Prime Coatings has been a leader in the industrial coatings business for over 25 years. In January of 2016, Prime saw an opportunity in paperless reporting for QP compliance, and their research led them to sign up with TruQC. After using TruQC successfully for three years, Prime opted to try a cheaper solution that promised many of the things TruQC already delivered. However, Prime quickly realized that less expensive meant less capable. Therefore, Prime returned to TruQC as a customer in 2019.

How is TruQC a better fit for your operation over the competition?
“TruQC is very easy to use, [even] for people who have little to no electronics background,” says Austin Moody, Project Manager at Prime Coatings. “The reports in TruQC are laid out much better than the competition.”
Usability is a huge factor when deciding whether a digitalization solution will work for your business. Prime found out very quickly that layout and report flow are key, which is why TruQC has always focused on a mobile-first approach. This means designing an intuitive user interface that lets field users collect data as they did previously with little or no disruption in process. Capturing data digitally in the field means reports are created while users are filling them out. By doing so, users eliminate the extra burden of compiling data and pictures into inflexible, outdated software once they are back at the office.
TruQC offers a number of ways to simplify reporting and improve efficiency, with a key feature being integrations with PosiTector and Elcometer devices – something the competition lacks. Any TruQC user can import environmental, surface preparation, DFT (dry-film thickness) and surface cleanliness readings directly into their reports using a Bluetooth or Wi-Fi connection without any data re-entry required.
“Plain and simple, the field personnel actually use [TruQC]. It is very easy to follow and there is no guessing when it comes to providing full and complete information. [The] other software was too difficult to navigate. TruQC reports and platform have a much better flow,” says Moody.
How does TruQC improve your business?
“Its biggest impact would be on the job documents availability to the office. TruQC provides quick and easily accessible job documentation [and] we are able to have a better idea of the day-to-day progress, quality and safety from the office,” says Moody.
TruQC makes it easy for users to complete their reports daily and also gives operations oversight without having to be out in the field or waiting on physical copies of reports. Prior to using TruQC, Prime’s workflow included paper reports coming into the office every few days or even weekly. TruQC’s ability to sync documents and reports in real time means all areas of operation are always up to date and reports and data move through workflows seamlessly.
And our platform is flexible. From the field user experience to corporate data requirements, TruQC can configure our solution to meet your unique needs. Should a client need additional reports or require a change in process, TruQC can digitalize it, with an open line of communication for customer input along the way. When asked about TruQC’s report customization compared to other software Moody responded, “TruQC has always been more than willing to customize reports to a contractor’s specific needs [and] the changes are done quickly as well.”
How does TruQC help comply with industry requirements?

As an industrial painting contractor, Prime Coatings must uphold certain standards, regulations and certifications in order to complete work, win projects and stay competitive and compliant. This means a lot of reporting and documentation to keep track of, including that which is required to stay compliant with industry standards set by organizations such as SSPC (Society for Protective Coatings) and NACE (National Association of Corrosion Engineers).
“TruQC works closely with SSPC and knows what we need as a contractor,” said Moody. “TruQC understands what is required by SSPC in the bridge painting world and provides most, if not all, reports necessary to the job.”
TruQC’s close relationship with SSPC and NACE, as well as our background in the industrial paint and coatings industry, means we nailed reporting for painting contractors. Once a client is signed up with TruQC, they will have immediate access to 13 standard, SSPC-endorsed reports. When reports are created, they are stored in TruQC’s File Cabinet that can be filtered by the job, report type, or creator, making audits a breeze.
All of Prime’s documentation that was previously stored in bulky binders is now in one centralized, digital location with TruQC’s Document Library. It now takes Prime little to no time for someone to pull up a training document or certification for reference during an audit. Because TruQC is cloud-based, all information can be updated immediately for all users, connecting the field users and home office more than ever.
“[We now] have complete and accurate information for all jobs located in on one platform.”
– Austin Moody, Project Manager, Prime Coatings
How would you describe your experience working with TruQC?
Our team is committed to supporting clients before, during and long after implementing TruQC. We make sure all questions, concerns and configuration requests are answered in a complete and timely fashion. So, when Prime signed up with us again, we were eager to know their thoughts on our on-boarding process, app training and customer support.
“TruQC does a great job of bringing new customers up to speed on their software, even though it is very user-friendly to being with,” commented Moody. “The staff at TruQC are prompt in their response and provide an excellent experience with their software. The TruQC staff are very easy to get a hold of, whereas the competition usually took a few hours or even a day or two to respond.”
When working with the other software company, Prime found they often had to ask for changes, but the time it took to even get a response felt like hours and dollars wasted. Since returning to TruQC, Prime was impressed by how quickly their account was up and running with all of their previous account data fully restored.
When we asked Prime to rate TruQC’s customer support compared to our competitors on a scale of 1-10, with 10 being excellent, Prime rated TruQC a 10, while only giving our competition a score of 5.
At TruQC, we want to see companies grow, and we think the best way to do this is to grow with them. For businesses to continually improve they must adapt and change. Why shouldn’t your digitalization solution do the same? Rather than being a plug-and-play solution, TruQC’s configurable platform, experience, and ongoing support allow for flexibility and savings, whether your business is big or small.
With TruQC, it’s not only possible, but it’s easy to digitalize your business, no matter where you start your digital transformation journey. When we asked Prime how their perception of TruQC has changed since becoming a customer, Moody responded:
“Paperless reports are the way to go. Using [TruQC] is much easier than collecting hard reports weekly and it’s nice to have electronic reports as the work is progressing. The competition is not where it needs to be to compete with TruQC. We may have been spending less money, but in the end, employees were not using other software due to difficulty.”
Thank you, Prime- and welcome back!
(SPOT Tracker and TruQC have joined forces to become TRU, a Jones Company)
Kalmar creates terminal automation and energy-efficient container-handling solutions for ports, terminals and distribution centers. The global company has 5,700 employees in 30 countries creating a variety of handling equipment ranging from empty container handlers and yard cranes to reachstackers and forklift trucks. For such a wide-reaching company, project management was a daunting task before TruQC. Finding a quality management system was important to increase efficiency and effectiveness.
Return on investment
Implementing TruQC took several months. During consultation, TruQC visited Kalmar on multiple occasions to provide demonstrations on how the app could be beneficial. Eventually, Kalmar chose to use the app and both sides identified 15 different reports to integrate.
When analyzing TruQC, Kalmar identified particular aspects as selling points on the app – document control, customization, TruQC’s customer support service and unlimited cloud storage. These aspects led to the development of the 15 reports Kalmar uses on a daily basis in their Production, Quality and Paint departments. This custom functionality has proven to be incredibly valuable to Kalmar’s return on investment.

Kalmar has used TruQC since 2016 and since then, they have seen a substantial return on investment. Kalmar implemented TruQC for 15 time-consuming forms that took anywhere from 12 minutes on the low end to a full hour on the high end to complete. Comparing these processes before and after TruQC, Kalmar has reduced labor hours by almost 41 percent. This has resulted in a net savings, in terms of dollars, of over 28 percent. Comparing the net savings to the fixed investment costs, Kalmar saw a 316 percent ROI in the first year of using the TruQC app.
Additional benefits from TruQC
With roughly 10 users in three different departments, Kalmar uses the app to improve documentation of its end-of-line test reports, pre-delivery inspection for assembly stations, final vehicle audits and documentation of continuous improvements.
The time savings reaped from using the application has been a notable perk, but the most recognizable benefit Kalmar has seen from TruQC is documentation control. The app makes all documents easy to locate, and with the unlimited cloud storage, all documents are up-to-date and available to those with access. There is no longer the risk of workers using tangible printouts of outdated documents. Additionally, the elimination of non-value added activity, such as redundant data transfer, has been a substantial help.
While there has been an extensive journey involved with implementing the application, the adjustment among users was swift and painless. Users quickly bought in and adapted to the changes during the testing phase and the results have been readily apparent.
Request an ROI estimate
To see what kind of return on investment your company could expect with TruQC, fill out our ROI estimate request form. Someone from TruQC will provide a consultation with you and gather additional information. We will use that information to calculate an accurate depiction of potential ROI should you implement TruQC.
“Our CEO has become a big advocate of the app, and when we have visitors, he proudly highlights its implementation as a staple of our culture of continuous improvement.” – Israel Cruz, Quality Manager, Kalmar Mobile Equipment
(SPOT Tracker and TruQC have joined forces to become TRU, a Jones Company)
ENLACE, a non-profit organization, helps churches in El Salvador, Nepal and the U.S. transform their surrounding communities with significant development projects. Their team of 50 members connect churches to sustainable community development projects and help partner churches with communities for mission trips and fundraising campaigns.
In 2016 alone, ENLACE completed 636 projects that served 217 communities, helping nearly 190,000 people. Seeing the wonderful work the organization was doing, TruQC felt strongly about ENLACE’s mission and chose to provide free access and support.
ENLACE is one of the smaller groups using the TruQC app, but a perfect example of how it’s great for small companies as well as big ones. The organization has a team of four TruQC users working throughout Santa Ana, Cara Sucia and Metalio, El Salvador and the U.S. The crew utilizes the app’s customer-specific workflows to guide their projects in a more productive manner.
What issues did ENLACE face before TruQC?
The most prominent issue ENLACE encountered was the collection and processing of community evaluation data. Original data collection efforts involved visiting each community and having exhaustive meetings with leaders in order to collect as much information as possible. Field staff would compile the collected data and send the findings to the home office in the U.S. While processing the information between the field and home office, ENLACE risked losing critical project information. Once all the information was obtained, it would be sent back to the home office in the U.S. for processing, creating gaps that increased the risk of losing imperative findings.
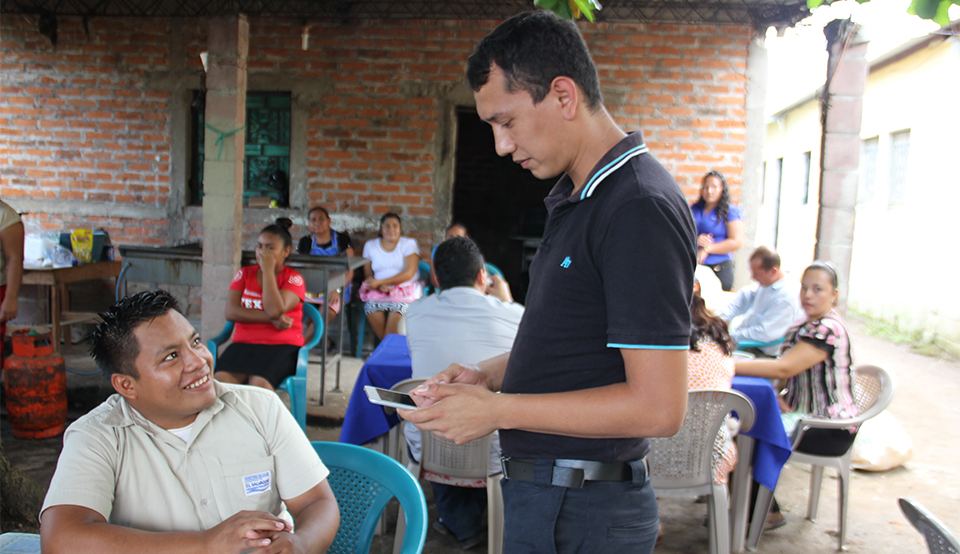
The execution processes for each project relied heavily on lengthy reports and exhaustive communication efforts. The lack of a real-time management system slowed the implementation and completion of community improvement projects. Any delay in health, infrastructure or economic development programs can have negative impacts for those reliant on the improvements these projects bring to the community.
Integration of the TruQC engine enables ENLACE to overcome these issues and deliver on its mission. TruQC’s real-time global syncing and configurable reporting capabilities allow users to quickly process immediate, up-to-date information from any location.
What has changed since implementing the TruQC app?
From the beginning, TruQC and ENLACE worked together to understand ENLACE’s specific business requirements and implement the app into their organization’s daily tasks.

Utilizing TruQC’s flexible, adaptable software, three custom reports were created for the monitoring and evaluation of community projects. With these reports, ENLACE now takes extensive notes and photos, provides detailed analysis and completes checklists to score their work and gather metrics on their building projects. With TruQC’s easy-to-use interface, time spent on reporting is significantly decreased. Furthermore, immediate report generation means reports are ready to be reviewed, approved and sent out immediately upon completion. Using TruQC’s document management solution, ENLACE has streamlined their evaluation processes and improved the way their organization monitors projects.
ENLACE users analyze objectives, strengths, self-management, costs, resources and more with TruQC reports. This gathered information is available in real-time, skipping extra efforts to transmit and process the data. Those working in El Salvador and those working in the U.S. offices are able to communicate with the same up-to-date information, resulting in a swifter execution of all projects. Projects can be approved from afar without any delay in communication. With TruQC’s real-time syncing and cloud-based software, ENLACE users can make informed decisions concerning a project – anytime, anywhere.
A key benefit ENLACE takes advantage of is the ability to translate TruQC back and forth between English and Spanish. This capability, combined with the clean and professional organization of each report, further reduces communication delays and mitigates risk of pertinent data getting lost or overlooked.
Helping throughout the implementation of the app was our technical support system. The organization relied on our support team to understand and use the app in conjunction with their needs. Our team is always willing to explain any step in the process, making integration run more smoothly.
All in all, TruQC has helped ENLACE mitigate evaluation and monitoring issues in the field while also improving internal communications.
“We think it is a really useful app that helps in our everyday reporting process and we would highly recommend it for others that are looking for this kind of support in their companies. The TruQC platform has worked incredibly well for us while implementing community development initiatives throughout rural El Salvador. TruQC makes the evaluation of our community development projects a breeze!” – David McGee, Communications and Partnership Development Director.
(SPOT Tracker and TruQC have joined forces to become TRU, a Jones Company)
Naval & Industrial Solutions (NIS) struggled with their paper reporting process — which made it hard to efficiently file, locate and edit reports. They recognized that to become the leading coatings inspection company in the Latin American market, they needed to find a way to take their reporting process paperless. The goal was to spend less time on reporting and complete jobs faster to see better returns on their work.
As an inspection company that does their reporting entirely in Spanish, no off-the-shelf reporting software would do. They needed a software company that could configure reports and offer training and support in fluent Spanish.
Turning to TruQC for streamlined reporting workflows
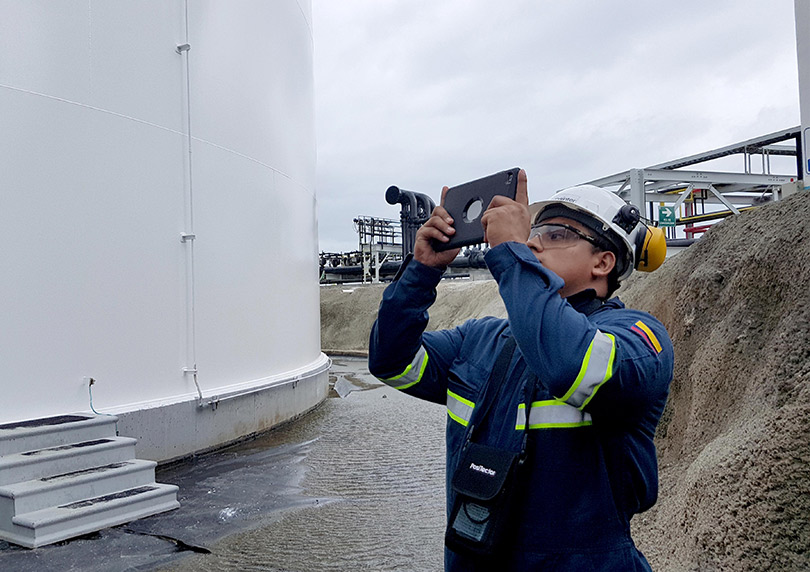
NIS turned to TruQC in order to minimize reporting time and improve field-to-office communication. TruQC’s bilingual capabilities helped ensure their team’s success in adopting and utilizing the app day to day.
TruQC’s impact at a glance
- Tank inspection times reduced by 50% — from a full day to half a day.
- Inspectors can instantly attach photos to reports — rather than tediously importing them in Word or Excel.
- Bilingual support from the TruQC team enables NIS to always get the help they need to get the job done.
- TruQC transformed stacks of paper reports into a cloud-based, searchable file cabinet.
Streamlined reporting and better return on inspections with TruQC
TruQC is a paperless reporting app designed to transform your proven processes into secure, digital workflows. Plus, the TruQC app and the support team behind it specialize in serving both English- and Spanish-speaking organizations, making it the perfect reporting solution for NIS’ needs.
Adopting the new software into NIS’ reporting workflows came with a learning curve at first. The initial training and bilingual support provided by the TruQC team, however, helped the NIS team quickly learn and adopt TruQC into their day-to-day routine. TruQC’s Project Managers worked with NIS to configure inspection reports and coatings surveys to each client and project’s needs, ensuring the software provided the most value to the NIS inspectors.
Juan Caballero, President of NIS (SSPC Master Coatings Inspector/NACE CIP Level 3 Bridge & Marine), credits TruQC as being incredibly user-friendly for inspectors in the field. When an issue does arise, he says TruQC’s customer support always resolves it quickly — even on holidays.
NIS’ field inspectors —who use the app entirely in Spanish— now complete inspections faster and more accurately with office employees overseeing all projects in real time. Inserting photos into reports is simplified with TruQC’s iPad camera integration, saving time over trying to embed a photo into an Excel or Word document. Tank inspections that used to take a full day can now be done in half the time and accessed by administrators immediately. That’s a 50% reduction in inspection time, directly affecting NIS’ bottom line.

The benefit of TruQC is about more than reducing inspection time, though. Caballero said that NIS is more confident in their inspections now that he can better manage field inspectors. With TruQC, he can give inspectors feedback on their reports as they are being completed. If there’s a simple issue, Caballero said he can fix it himself. When he needs to reject an inspector’s report and have them correct it, he can easily communicate that within the app, saving significant back and forth time.
Once reports are approved and complete, all data can be accessed and queried in TruQC’s secure, cloud-based file cabinet — rather than searching through stacks of paper reports. Overall, NIS is now able to complete, correct and approve inspections faster and more accurately with improved communication between the field and the office.
Regardless of your organization’s continent or industry, TruQC has the potential to drive efficiency in your reporting process. Let’s talk about how our team can configure our software to fit your proven reporting workflows.
Vigor Industrial, a leader in shipbuilding and repair, experienced serious reporting difficulties on the USS Gridley project. Objective Quality Evidence (OQE) deadlines were missed. 62 Corrective Action Requests (CARs) were raised by the Navy — and 60% were coatings / OQE related. 480 hours were spent cleaning up paperwork discrepancies. Vigor needed to streamline their processes, ensure greater accuracy and reduce corrective action requests.
Before commencing their next Navy project —the USS Kidd— Vigor overhauled their quality assurance (QA) program. One of those changes was taking their reporting process and workflow paperless with TRU. The result? Zero CARs, a clear audit trail and a “consistent, clean and quick” OQE review process.

Vigor took a three-pronged approach to optimize their QA program and reduce Corrective Action Requests before the USS Kidd project:
- Use third-party inspectors for greater objectivity.
- Take inspection authority away from subcontractors.
- Leverage TRU for document management and reporting.
Employing third-party inspectors and removing the subcontractors’ inspection authority gave Vigor greater control over the OQE review process. This also streamlined the process because subcontractors couldn’t go directly to the government — and Vigor was able to schedule and conduct preliminary inspections before calling in the Navy.
TRU’s impact at a glance
- Without TRU: 62 CARs. With TRU: 0 CARs.
- Fewer than 15 admin revisions made on USS Kidd project.
- TRU eliminated 480 hours of review time.
- Consistent, clear, accurate OQE packages handed off to the Navy.
Integrating TRU results in a smoother review process
Vigor has been building and repairing ships to a high level of quality for years — and they didn’t need to reinvent their proven workflows. Instead, they needed a reporting solution that optimized the accuracy and speed of their existing processes while reducing corrective action requests submitted by the Navy.
That’s why they turned to TRU — a paperless reporting application that transforms existing reporting processes into secure, digitalized workflows. TRU collaborated with the National Shipbuilding Research Program (NSRP) to build out the eight appendices for NSI 009-32, making TRU the perfect tool for meeting the strict compliance requirements of the U.S. Navy.
On-site training and support from the TRU team
As Vigor was first implementing the software, the TRU team provided on-site, hands-on training sessions. This lowered the learning curve and allowed the Vigor team to ask questions.
The USS Kidd Navy team was included in these sessions. This helped to establish expectations and allowed the Navy to give input into how TRU would be used on their project. Several ship building specialists from the USS Gridley team also were present, offering insight into the process problems TRU was aiming to fix.
All standard items and specifications available within the app
TRU eliminated the need to carry binders of documentation in the field. All applicable documents —specifications, standards such as NSI 009-32 and all reports and appendices— were contained within the TRU’s Document Library. And because TRU automatically syncs to the cloud when a connection is available, inspectors had up-to-date access to every document they might need both in the office and the field.
“I can’t even put a dollar sign on my ROI because it was that drastic.”
That’s what Lindsay Docherty, Director of Quality Assurance at Vigor Industrial, said after implementing TRU. Even the ship building specialist on the USS Kidd project, Mark Donaldson, said the “review process for OQE packages is consistent, clean and quick” with TRU.
TRU allowed Vigor’s inspectors to conduct preliminary inspections on the iPad before bringing in the Navy, minimizing admin errors. Plus, all applicable documents were readily available within the app to be included in the appendices.
Implementing TRU didn’t come without its challenges — namely that the Code 132 / QA team wasn’t present at the initial training and as a result was hesitant to embrace the new technology. However, after seeing TRU’s success on the deck plate they were willing and eager to utilize the tool, further proving the project a resounding success for Vigor.
Looking forward: Leveraging TRU on the USS Sampson
The USS Kidd project is now complete, and the results are in: no OQE packages were returned due to admin issues and no CARs were raised by the Navy. Now, Vigor is using TRU on the $42.2 million USS Sampson project.
To learn more about TRU and its potential to promote accuracy, efficiency and compliance across industries, request a consultation with our team. We’ll discuss how we can configure our reporting software to your proven workflows — and how it can drive down cost and risk throughout your organization.
(SPOT Tracker and TruQC have joined forces to become TRU, a Jones Company)
Blastco, a TF Warren Company, is an industrial abrasive blasting and protective coatings subsidiary. Its roots are based in field applications for above-ground water storage tanks. Since the early years, Blastco has come to specialize in the application of protective coatings and linings to an array of substrates such as dams, silos, wastewater treatment plants and petrochemical tanks.
Utilizing the latest technology is one of the ways Blastco stays at the forefront of the high performance protective coatings and abrasive blasting industry. Their employees use TruQC to ensure quality control on every project. From paperless documentation to field communication and reporting, TruQC has improved many of the processes at Blastco.
TruQC’s benefits to Blastco operations
Early usage of the TruQC app was specifically for quality control and safety reporting. That has since expanded to daily use for production, timesheet and expense reporting. The app has made document reporting, project management and recording man-hours especially easier.

Since implementation of TruQC, the single most recognizable benefit Blastco has seen is the ability to monitor projects in real time. With the use of cloud-based reporting, employees can review and approve paperless documentation on all projects as the job is progressing. This ability saves tremendous amounts of administration and review time.
The employees’ reaction to change management
From the beginning, employees were very receptive to the change. TruQC was rolled out to users with almost no push-back. Whether it was a technology savvy employee or a coworker who had never sent an email, the entire company was very open-minded and learned the system quickly.
Valuable tech support
One of the most prevalent benefits has been the technical support TruQC employees provide. “Support has always been one of the best aspects of the system,” said Jeremi R. Day Sr., Blastco Quality Control Manager. “I’ve never had trouble contacting anyone or getting any support I need – everyone has always been extremely helpful and accessible.”
By integrating the TruQC app, Blastco has streamlined their project management processes, increased efficiency and improved communication.
(SPOT Tracker and TruQC have joined forces to become TRU, a Jones Company)
A leading pipeline coating contractor puts quality control software to work
A commitment to innovation is very often the hallmark of a good company. Especially in a field that’s marked by a stiff competitive landscape and rapid change brought on by new technologies, as is often the case in industrial services. But what makes a company truly great, and makes it stand apart from its competitors over the long term, is such a passionate vow to innovation and doing things “the right way” that it doesn’t veer from these principles even when it’s on top.
And in a lot of ways, Apache Industrial Services is among the top in the industrial painting industry. The Houston, Texas-based industrial services company opened a 125-acre campus last year, massively expanding their shop application of pipeline coatings for clients in the oil production industry, both upstream and down. They found that by shop-applying pipeline coatings they were able to execute jobs for their customers at a 20-30 percent lower cost than in the field. As such, they decided on large-scale growth in the equipment and production space that would ensure they could accommodate a wide range of projects. Apache’s Houston Operations Center, the largest shop-coating facility on the Gulf Coast, perfectly demonstrates Apache’s commitment to innovation and expansion, but it’s not the only noticeable sign of its adherence to these principles.
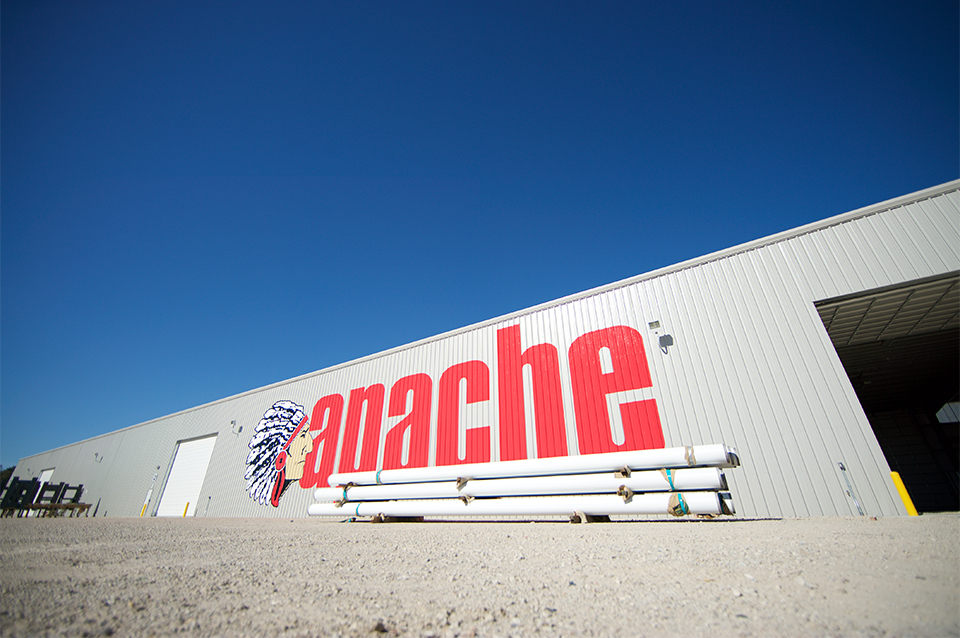
Apache’s road to such high esteem within the industrial services community is about more than their 300,000 square feet of production warehouse space, but about their willingness and capability to constantly improve their business, whether through new ideas, tactics or technologies.
And one can’t talk about Apache without talking about safety. For instance, their invitation to a journalist from CoatingsPro Magazine to a weeklong safety seminar led by top Apache brass at their Houston headquarters in late 2012. This is just one example of the company’s level of transparency when it comes to safety both in the field and in the shop. Additionally, they encouraged employees to bring along a photograph of their reasons for avoiding injury to that seminar, adding a tangible tinge to what remains for some companies an abstract ideal.
What makes Apache stand out from their peers is their dedication to constant improvement. As it happens, in 2011, another company set out to shake up the industrial painting industry, but they set out to partner—rather than compete—with innovators like Apache. TruQC was founded exactly with relentless improvers like Apache in mind. They imagined a better version of quality control for companies willing to step outside the box and brave enough to embrace new technologies.
Keeping an industry honest
TruQC was created for companies who place an emphasis on strategic growth and continuous commitment to process refinement. Meant to address inefficiencies and loopholes in the reporting process, it was designed to be a tool for companies that wanted to do things a better way, even if they were doing them pretty well already.
Built for the iPad and web, TruQC is cloud-based, so real-time syncing keeps all of its users on the same page on any given project, whether in the field or the home office. TruQC’s inspection device integration ensures the accuracy and verifiability of inspection measurements. And intuitive data storage and retrieval methods address the issues that used to arise when keeping an enormous amount of physical paperwork on hand, sometimes in unforgiving environments,
Safety was an important priority for TruQC from the outset as well. Certain features of the app perform specifically to make it more difficult for users to skirt industry-standard safety measures and to make it easier for contractors to voluntarily commit to better record keeping and safety training. It was also meant to encourage inclusive dialogue between management and employees within industrial services companies. For jobs like the coating and lining of oil and gas pipelines, where both human and environmental safety is on the line, TruQC was meant to play a role in mitigating potential dangers arising from cutting corners in quality control.
“When we started TruQC, we were a little dismayed at some of the liberties we were seeing being taken when it came to industrial painting and essential documentation,” said TruQC CEO, Ross Boyd. “So we knew from the outset that we were looking for clients who were committed to integrity and believed strongly in the best practices that were designed by the industry, especially where quality work is as essential as it is on pipelines. In that sense, Apache was an ideal client long before we started working with one another.”
When integrity and innovation are more than just buzzwords—and truly drive the direction of a company like Apache Industrial Services—TruQC is there to help put that commitment into action. And on numerous pipeline coating projects since the companies began working together, the tangible benefits have included less time spent on quality control documentation, increased transparency and an enhancement of Apache’s reputation for delivering projects on schedule.

TruQC and Apache Industrial Services
Apache has used TruQC’s quality control software on a number of pipeline projects since they began using TruQC in September of 2014. Following training, Apache crews found that they were able to execute the same documentation tasks they had before, in a fraction of the time.
“The ability to manage different coatings systems, access isometric drawings for verification purposes and reference line lists, all while conducting and releasing hold point inspections, has allowed for a more expeditious inspection process and enhanced the projects overall,” said Cathey Perkins, Vice President for Quality Assurance at Apache.
TruQC’s permission-based workflow process also makes it easier on Apache’s quality control inspectors to keep reports moving along the approval pipeline. Its core chain-of-command workflow was built with quality control inspectors in mind, and it can be customized to match the internal workflows common to companies like Apache and for pipeline projects in general. This adds further efficiency to a process that’s been subject to miscommunication in the past.
Communication between Apache and their clients has also improved while using TruQC. Objective reporting metrics like time, data, GPS and signature stamps all help to increase transparency when reports are passed between Apache and the project owner. The app is also able to provide further clarification when communicating project details by allowing photos and annotated drawings to be included with reports.
According to Apache, TruQC has enabled them to consistently produce a more comprehensive and representative inspection report for pipeline coating projects than without the software and in a fraction of the time. Apache estimates that using the software to input inspection data saves on average one to 1.5 hours per day per quality control inspector. Smart field population of repetitive data and dropdown field pickers are the type of efficiencies that, when considered against the salary of a full-time staff member, can lead to significant return on investment.
It seems that the days of filling out reports in the cramped cab of a truck while inspecting pipeline projects also won’t be missed by Apache quality control staff. Especially on jobs that take crews far from the home office, the app’s ability to act as a virtual, portable file cabinet, and drastically reducing the need for physical paperwork, is seen as a blessing.
“The ability to carry simply a tablet and inspection equipment has not only increased efficiency of the inspection process, but lessened the opportunities for coffee stains on reports, missing logs and the inevitable procrastination resulting from needing to wait to complete reports until later,” Perkins said. “The scope of work, specification, product data sheets, safety data sheets, drawings, and technical notes can all be stored on the tablet for immediate reference, eliminating the amount of paperwork to organize and keep track of on a daily basis.”
The Daily Inspection Report is a favorite among Apache staff for its ability to document project-critical measurements and ensure compliance with regulatory standards. Apache also now uses the software to keep track of daily timesheets. But, predictably for those familiar with Apache and its reputation, they’re also taking the opportunity to use TruQC as a documentation tool to enhance overall crew safety. Reports such as TruQC’s Toolbox Talk Report are available to document safety and training meetings, where attendance can be logged, associated documents stored and site safety surveys conducted.
Conclusion
When a company truly commits to continued growth, it doesn’t stop looking for a better way to do things. It’s exactly those types of companies TruQC set out to assist. There’s a better way to approach quality control, both in the shop and in the field. On pipeline projects for Apache Industrial Services, we’ve drastically reduced the amount of time quality control staff spends filling out paperwork, allowed them the freedom and mobility to do it from anywhere, and enhanced transparency and communication between parties.
(SPOT Tracker and TruQC have joined forces to become TRU, a Jones Company)
“The thoroughness of the documentation, the organization, the ability to import photographs and drawings and so forth has improved the quality of our documentation considerably. So we’re very enthused about using it and hope to even more in the future.”
– Bruce Rutherford, Coatings Group Manager, KTA
Making the experts even better
KTA-Tator, Inc. knows quality control. And there’s no higher endorsement than when the experts are using your tools to become even more…expert. So when KTA, one of the most trusted third-party inspection firms in the country, put TruQC to the test we knew it would give us a pretty good idea of where we stack up.

After initially signing up a small number of users (As we often suggest. See this post for more on implementing our software.), KTA decided to drastically scale up the number of inspectors using our software this year. Now, two of KTA’s five business units use TruQC, adding close to 100 total users.
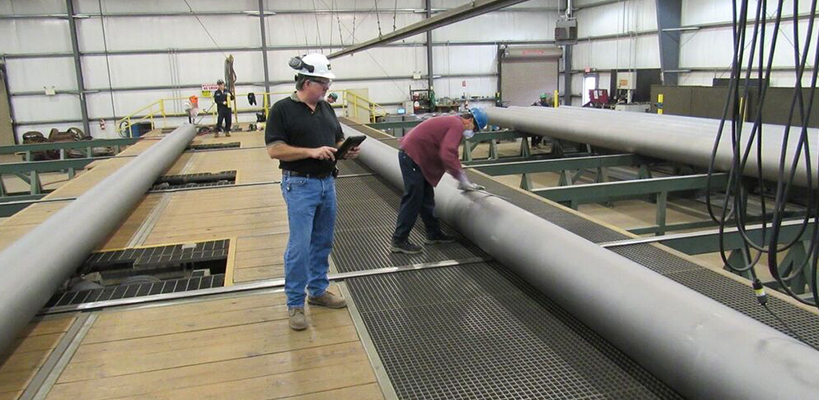
Out of the office and onto the job site
Before using TruQC, KTA inspectors were reporting with templates that were made using word processing software. Inspectors were spending a lot of time completing the forms using laptops in the office. Their template could accommodate images, but the formatting was notoriously finicky, which led to extra time filling out reports.
All in all, workarounds and inefficiencies were leading to KTA staff spending more time in the office than they really wanted to. An ideal reporting solution needed to allow KTA inspectors to spend more time interacting with owners and contractors in the field. It should also allow them to easily add images and drawings associated with their comments, while still preserving all the data fields specific to KTA operations.
The solution couldn’t be an out-of-the-box one. It had to address KTA’s issues, without completely scrapping the template they had perfected through years of experience.
A reporting solution to call their own
What we delivered:
- The ability to seamlessly insert supporting images on reports, without wasting time with formatting issues. A core feature of TruQC, photo documentation allows KTA inspectors to associate images with comments on surface preparation, completed painting projects and issues that they would like to bring to contractors attention in the future.
- More time spent in the field. ““I think the owners appreciate that our inspectors are spending less time in the office working on a report,” said Bruce Rutherford, Coatings Group Manager at KTA. “Now, with their iPads, they’re mobile and report on the fly. They’re in the field more with the contractor doing the actual work.”
- A configured template, designed based on the needs of KTA inspectors, so they weren’t starting from scratch with new documentation. Inspectors recognized and could find the fields they’d been filling out all along, but this time with added capabilities and consistency.
- An edge when it comes to bidding alongside the competition. KTA is now able to explicitly detail the information their inspectors will deliver, and the format it will be delivered in, prior even to winning a job. “It gives us a competitive advantage over other companies bidding for the work,” Rutherford said. “It’s received very favorably in short-list presentations. Everyone’s impressed that we’re able to demonstrate the software beforehand, in real time.”
(SPOT Tracker and TruQC have joined forces to become TRU, a Jones Company)
“A Spartan knows his or her flaws as well as his or her strengths.”
It’s a core tenant of one of the most recognizable fitness brands on the planet, a level you don’t get to without recognizing where you have room for improvement. So, when Spartan Race, an obstacle race and fitness lifestyle brand, noticed they were spending a little too much time filing quality management documents with spreadsheet software, and were having trouble attaching photos, they began shopping around for a software fix.
When you run 130 obstacle races annually around the world, with between 20 and 60 obstacles per race that are made up of fire, metal and mud, there’s plenty to keep track of. So Spartan came to TruQC to see if we could help them out with quality management. In the end, we were able to configure the software we originally built to help with industrial painting to help one of the world’s premier race organizers guarantee they deliver the same quality experience to challengers all over the globe.
We recently had a chat with Spartan to find out a little more about how they use our software.
Could you briefly discuss how Spartan uses TruQC?
Spartan uses TruQC to report on the overall operations for US and international races. Each Quality Manager uses the reports to measure the quality of the events and determine what improvements need to be made.

Given that TruQC started out as an app for industrial painters, how did Spartan decide that it could be useful to your operation?
We had been using Excel spreadsheets for our quality management reports and would attach photos in DropBox. The process for each report would take hours and, in the end, the Excel sheet and separate photos didn’t form a cohesive report for our licensee. We looked for a better solution and found that TruQC mirrored what we needed (with a few configurations).
Do you use TruQC at all your races? How many user accounts does Spartan have?
We don’t use TruQC at all of our races. It is used at several international and U.S. each year (probably a total of 40 times), as the Quality Managers do not attend every race. We currently have 6 user accounts.

Could you describe the process of getting Spartan staff started with TruQC? Were there any problems with learning the software or any staff members who especially had trouble?
We had a very easy transition. A TruQC representative met us at one of our conferences when we were all together so we had the benefit of receiving hands-on training. We didn’t really experience any users who had trouble. The most common problem we have is forgetting our passwords.
What sort of efficiencies has Spartan gained by using TruQC? Are any tasks especially easier now that you’re using TruQC? Have you collected any data that might back this up?
Our quality managers are able to use their time more efficiently in producing their reports. Spartan Race is able to track the scores for each country/market and measure the progress (or lack of). This has helped us get a better understanding of each category by country and how each market is progressing in producing quality events.
Anything else you would like to add about TruQC that we didn’t ask about?
We are really happy with the software and love using TruQC to help us to do our jobs better.